Blow molding mainly includes extrusion blow molding (EBM), injection stretch blow molding (ISBM) and injection blow molding (IBM). It is a molding process specially used for mass production of hollow plastic containers. This issue introduces three types of blow molding process: extrusion blow molding (EBM).
Process cost: processing cost (medium), single piece cost (low);
Typical products: container packaging for chemical products, container packaging for consumer goods, and container packaging for drugs;
Suitable output: only suitable for mass production;
Quality: high quality, identical wall thickness, surface treatment suitable for smooth, frosted and textured;
Speed: fast, 1-2 minutes per cycle on average.
Blow molding is divided into three categories
1. Extrusion blow molding (EBM): The cost is the lowest compared with the other two types, and it is suitable for the production of plastic (PP, PE, PVC, PET) hollow containers with a volume of 3 milliliters to 220 liters.
2. Injection blow molding (IBM): to be continued.
3. Stretch blow molding (ISBM): to be continued.
1. Extrusion blow molding (EBM) steps:
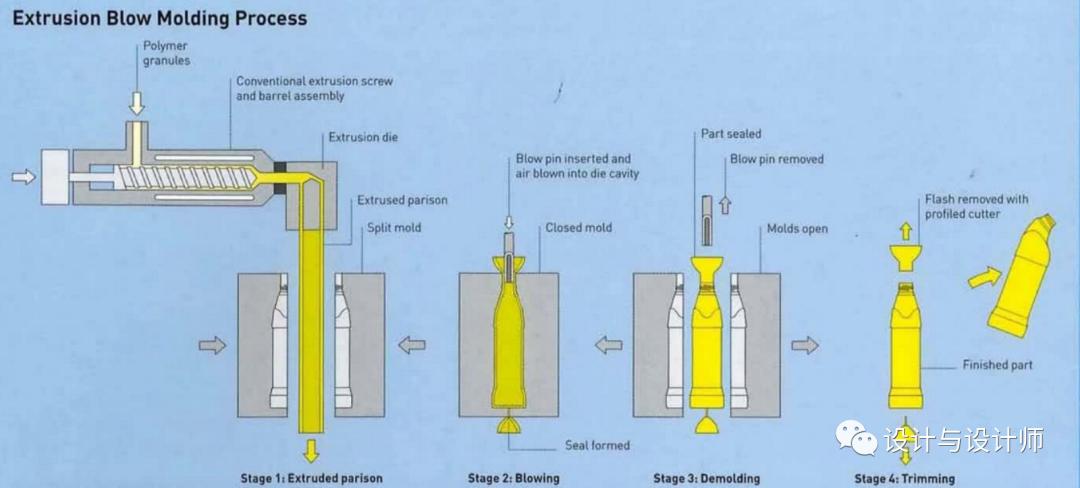
Step 1: pour the polymer particles into the hard mold, and form a colloidal hollow column-shaped prototype through heating and continuous extrusion of the mandrel.
Step 2: When the hollow cylindrical prototype is extruded to a certain length, the molds on the left and right sides begin to close, the top of the prototype will be cut by the blade to the applicable length of a single piece, and the air will be injected into the prototype through the inflatable rod to make the prototype close to the inner wall of the mold to cool and solidify to form the desired shape.
Step 3: After the cooling is over, the molds on the left and right sides are opened and the parts are demoulded.
Step 4: Use the repair tool to trim the part.
Post time: Mar-21-2023